Monolithic Isolation Joints - What are They?
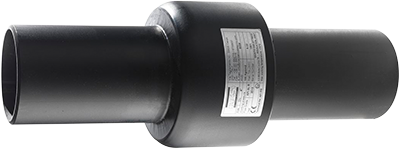
Click here to download our PDF brochure on IJ's.
Corrosion destroys approximately 20% of the worlds annual production of steel. Pipelines, which are mostly buried for the conveyance & distribution of gas, water & other hydrocarbons are particularly prone to corrosion - which can result in serious consequences. Typical examples are as follows:
- Conveyed-product leaks - at times accompanied by explosions & fires when gas or other hydrocarbons are involved;
- Contamination of water being conveyed in pipelines;
- Pollution of the soil, streams, waterways & shallow or deepwater estuaries;
- Interruption to services resulting in high equipment replacement & installation costs;
- Reducing the pressure rating of the pipeline as a result of deterioration caused by corrosion.
These costly drawbacks and damages could be avoided if pipelines were provided with effective cathodic protection. However cathodic protection could only be effective if the pipelines were:
- Provided with a high quality insulating coating throughout;
- Not in physical contact with unprotected foreign metal structures, including all related works which contain, protect, weigh down, anchor & support them;
- Electrically insulated from those parts that constitute a low-resistance earthing as well as from their sections or equipment which need not or cannot be cathodically protected.
The electrical insulation on pipelines is achieved by means of special fittings referred to as Isolation joints. The hydraulic sealing and the resistance to mechanical and thermal stresses of these joints should be at least equal to those of the relevant pipeline.
PCA has been engaged in the research & development of Isolation joints since the beginning of its activities in the anticorrosion field over 30 years ago. The main concern of PCA has always been to offer Isolation joints free from any mechanical & electrical inconsistencies so typical of traditional Isolation flange joints.
The technical characteristics of PCA Isolation joints are reflected in the high quality standards maintained throughout their design & manufacture. PCA Isolation joints offer the highest design reliability in a working environment because they are:
- MONOLITHIC - i.e. the assembly cannot be separated without being destroyed;
- Prefabricated & assembled in the factory shop making it possible to ensure the integrity of the homogeneous technical characteristics;
- Made up of metal components sized in compliance with the most advanced engineering & technical methods;
- Assembled with insulating components of the highest mechanical, electrical and thermal resistance. Their high resistance to internal pressures, to applied voltage and surface electrical discharges remains unaltered with time;
- Provided with an epoxy lining, applied throughout integral metal surfaces whose length and thickness are such that they give an excellent electrical resistance on the joints, even in the presence of water;
- Internally & independently tested to the strictest standards so as to offer the best warranty possible to the customer;
- Assessed with success by worldwide engineering specialists & distributors surpassing all severe technical quality testing during their extensive working life.
Because of their intrinsic properties, the various types of PCA Isolation joints need neither maintenance nor replacement during the entire working life of the pipeline on which they are installed. This provides substantial economic advantages since it allows for great reduction both in installation and running costs. In fact, whilst Isolation flange joints have to be installed above ground or within a water-proof inspection pit - PCA Isolation joints can be buried in soil (with appropriate external insulating coatings or wrapped with a suitable tape system).
|